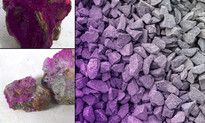
Le volume de déchets générés par la déconstruction va devenir très important dans les prochaines années. Que préconise l'Ifsttar et pourquoi ?
Les granulats constituent la partie la plus importante d'un béton, environ les 2/3 de la masse, et la fabrication de béton représente en conséquence environ 40 % de la consommation totale actuelle en granulats. Il s'agit également d'une ressource non renouvelable, de plus en plus difficilement accessible. La région Ile de France importe près de la moitié des granulats qu'elle consomme (environ 13 millions de tonnes par an, source livre blanc UNPG) et on estime que cette consommation va encore augmenter de 5 millions de tonne par an (source DRIEE Ile de France) avec les projets du Grand Paris. Dans un tel contexte, réussir à fabriquer du béton en économisant les granulats est un enjeu majeur.
En parallèle, le volume de déchets générés par la déconstruction des bâtiments et infrastructures en fin de vie augmente, et va devenir très important dans les prochaines années. En effet, les bâtiments construits entre 1950 et 1980 arriveront prochainement en fin de vie et les volumes de bétons à recycler produits seront alors très importants.
Actuellement, ces déchets sont traités en région parisienne de deux façons, soit par l'enfouissement, soit par le recyclage en matériau de remblai à faible valeur ajoutée pour les terrassements routiers. Avec l'arrivée prochaine de volumes de déchets plus importants, la filière routière ne pourra pas absorber ces déchets, dont le coût environnemental de traitement va donc augmenter de façon importante.
En France, le projet national Recybéton, qui regroupe des industriels et des centres de recherche comme l'IFSTTAR, a pour objectif d'accroître la réutilisation des matériaux issus des bétons de déconstructions en les utilisant comme des granulats pour la fabrication de nouvelles constructions.
Des problèmes techniques subsistent cependant dans les approches existantes de recyclage des bétons dans les bétons. Les granulats issus du concassage d'un béton présentent une porosité supérieure aux granulats naturels et des propriétés mécaniques inférieures. Par ailleurs, un obstacle majeur réside dans le mode de production des bétons à base de granulats recyclés. L'absorption d'eau de ces granulats est forte (entre 5 et 10%) et lente (elle a lieu sur une période de l'ordre d'une vingtaine de minutes). Un béton de granulats recyclés malaxés dans des conditions traditionnelles voit ainsi son ouvrabilité (aptitude à la mise en oeuvre) fortement chuter lors de la phase de transport du matériau.
Dans ce cadre, l'IFSTTAR a étudié la possibilité d'utiliser le phénomène de la carbonatation des bétons de démolition en vue d'améliorer leurs caractéristiques. La carbonatation est un processus naturel d'absorption de CO2 au sein du matériau, par carbonatation des hydrates de ciment présents dans ces déchets concassés. En effet, lors de la fabrication du ciment Portland à partir de calcaire et de silice, on réalise par cuisson du calcaire en présence de silice, la décarbonatation du calcaire. Cette réaction qui se produit lors de la fabrication du ciment est fortement émettrice de CO2. La réaction d'hydratation engendrée ensuite, entre le ciment produit et l'eau lors de la fabrication du béton, conduit à la formation d'hydrates. Ces hydrates sont à l'origine de la résistance mécanique du béton. Cependant, ces composés ne sont pas totalement stables mais seulement métastables : en présence du CO2 atmosphérique, la carbonatation des hydrates se produit naturellement et les hydrates, en réabsorbant le CO2, se retransforment lentement en calcaire et gel de silice, bouclant ainsi le cycle minéral.
Cette réaction est néfaste pendant la phase de service d'une structure en béton armé car en abaissant le pH du béton elle conduit à la corrosion des armatures en acier qui renforcent le béton. Mais, une fois la structure arrivée en fin de vie, elle peut être utilisée comme un atout, notamment dans l'optique de recycler le béton. Ainsi, la première conséquence que l'on en retire est l'amélioration de la qualité des granulats produits par les bétons de déconstruction. La seconde est le stockage du CO2. Celui-ci a pour effet d'améliorer le bilan environnemental du matériau béton. Les travaux de recherche menés montrent donc que la carbonatation de la matrice cimentaire du béton engendre un matériau dont l'absorption d'eau est à la fois plus faible et plus rapide que le matériau issu d'un béton non carbonaté, ce qui le rend beaucoup plus adapté au procédé traditionnel de fabrication du béton.
Pour mener cette carbonatation, deux voies de traitement ont été étudiées : la carbonatation naturelle et la carbonatation accélérée.
La carbonatation naturelle
Ce phénomène repose sur le contact entre le CO2 contenu dans l'atmosphère et le ciment. La première solution pour améliorer la cinétique de la carbonatation porte sur l'augmentation de la surface de contact en réalisant un concassage du béton de démolition. En transformant par exemple un élément en béton armé de type dalle d'une épaisseur de l'ordre de 20 cm en granulats d'environ 1 cm, la surface de contact offerte au CO2 atmosphérique se trouve multipliée par environ 1000. Nos résultats montrent qu'il est possible, pour des bétons traditionnels de bâtiments des années 50-80, de capter 50 à 60% du CO2 émis lors de la décarbonatation du calcaire. En intégrant dans l'analyse l'énergie utilisée pour le broyage et le transport du matériau, on montre qu'un tel traitement permettrait de piéger entre 15 et 20 kg de CO2 par mètre cube de béton traité. Il demeure cependant que la période nécessaire pour cette carbonatation est longue et rend nécessaire un long stockage du matériau avant réutilisation, de l'ordre de plusieurs mois, ainsi qu'un espace de stockage ce qui peut s'avérer prohibitif en pratique.
Carbonatation accélérée [1]
Il est possible d'accélérer le processus en travaillant à des pressions plus importantes, voire avec du CO2 supercritique (Figure 1). On parle de fluide supercritique lorsqu'un fluide est chauffé au-delà de sa température critique et lorsqu'il est comprimé au-dessus de sa pression critique. Les propriétés physiques d'un fluide supercritique (densité, viscosité, diffusivité) sont intermédiaires entre celles des liquides et celles des gaz. Le CO2 devient supercritique pour une température supérieure à 31 °C et une pression supérieure à 73 bars. Il est donc relativement facile à obtenir, est sans danger (non inflammable, non toxique) et est déjà utilisé avec succès dans l'industrie agroalimentaire, par exemple pour décaféiniser des grains de café, extraire des arômes de plantes à parfum ou encore dénicotiniser du tabac.
Des essais préliminaires effectués en collaboration avec le laboratoire de génie chimique de l'Université de Toulouse ont montré qu'on pouvait carbonater des matériaux cimentaires en conditions supercritiques sur 1 cm en une dizaine de minutes (Figure 2). Ce traitement a l'avantage d'être efficace aussi pour les fractions fines (sables) issues du recyclage et qui détiennent un potentiel élevé de piégeage de CO2. Celles-ci ne sont actuellement pas réutilisées dans la refabrication du béton car trop poreuses. Toutefois, le bilan socio-économique du procédé reste à réaliser. Il comporte un risque de déséquilibrage par un surcoût technologique important. Ce bilan dépendrait également du prix de la tonne de CO2 et de la mise en place d'une taxation sur le carbone.
Aussi ces travaux de recherche ont porté sur l'étude d'une variante plus simple à mettre en oeuvre et moins couteuse. Elle consiste à placer les granulats à pression atmosphérique mais dans une atmosphère contrôlée et enrichie en CO2. En quelques jours, on arrive alors à carbonater une couche de granulats recyclés de l'ordre de 10 cm. On peut donc imaginer qu'un bullage de CO2 conduisant à une pression partielle de CO2 élevée dans un « big bag » de granulats recyclés pourrait permettre de traiter les granulats en 2 ou 3 mois.
En parallèle, un modèle de carbonatation applicable sur des matériaux granulaires a été développé. Ce modèle permet de modéliser les phénomènes décrits plus haut, et notamment de prendre en compte la teneur en eau des granulats, paramètre majeur du phénomène de carbonatation (le CO2 pénètre en effet dans le béton sous forme gazeuse puis, pour réagir, doit se dissoudre dans le liquide interstitiel du béton). Le modèle permettra d'optimiser les temps de contact entre les granulats recyclés et la concentration en CO2 selon la teneur en eau des matériaux ainsi que leurs caractéristiques microstructurales.
[1] Références :
Gobert et al., Accelerated carbonation of hardened cement samples using supercritical CO2, 14th European Meeting on Supercritical Fluids Marseille, 2014
Thiery et al., Cinétique de carbonatation d'un lit de granulats concassés de matériaux cimentaires, Journées ouvrages d'art, Marseille, 2011.
Thiery et al., Carbonation kinetics of a bed of recycled concrete aggregates: A laboratory study on model materials, Cement and Concrete Research 46 (2013)
Belin et al., Cement paste content and water absorption of recycled concrete coarse aggregates, accepted for publication in Materials and Structures, 47:1451-1465 (2014)